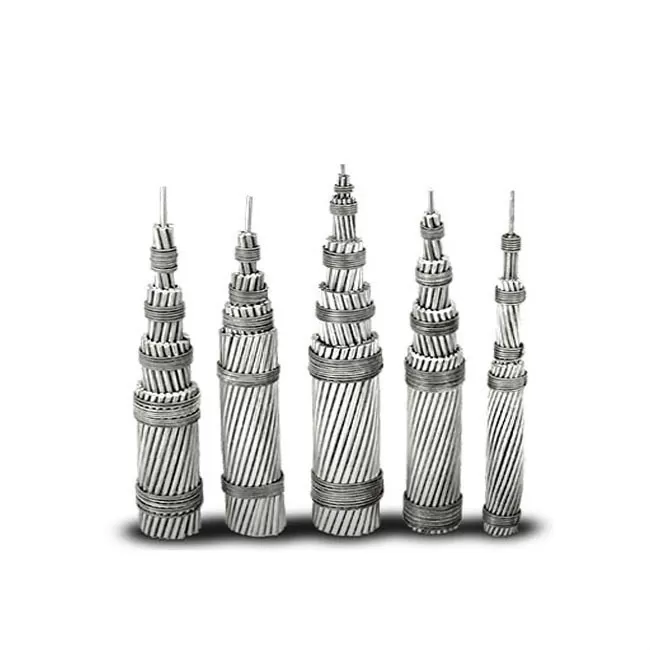
Introduction
AAAC conductors are made from high-strength Aluminum-Magnesium-Silicon alloy. Compared to ACSR, AAAC offers lighter weight, comparable strength, lower electrical losses, and superior corrosion resistance. These properties make AAAC widely accepted for distribution and transmission lines.
Conductivity
AAAC’s conductivity is measured in IACS (International Annealed Copper Standard). AAAC conductors typically have a minimum conductivity of 52.5% IACS, meaning they have 52.5% of the conductivity of pure copper.
Key Features
- High Strength-to-Weight Ratio: Robust mechanical support without excessive weight.
- Better Sag Characteristics: Reduced sag under load due to higher strength.
- Improved Electrical Properties: Lower electrical losses than ACSR.
- Corrosion Resistance: Excellent performance in corrosive environments, making them ideal for coastal areas.
Construction
AAAC conductors are made from several aluminum alloy series, primarily the 6000 series (Al-Mg-Si). These alloys are solution heat-treated for improved strength and can be either heat-treated or cold worked.
6000 Series Aluminum Alloys
- 6201 Aluminum Alloy: Used for electrical conductors and fuses.
- 6061 Aluminum Alloy: Suitable for heavy-duty structures such as bridges and aerospace components.
- 6063 Aluminum Alloy: Common in architectural applications like windows and doors.
- 6082 Aluminum Alloy: Used in high-stress applications like trusses and cranes.
7000 Series Aluminum Alloys
These alloys have the highest strength among aluminum series due to the addition of zinc, magnesium, and copper. They are not used for conductors due to their lower conductivity (max 36.71% IACS) but are used in high-strength applications such as aerospace and sports equipment.
Example Models
Here are some specific AAAC conductor models along with their electrical and structural parameters:
Model | Diameter (mm) | Cross-sectional Area (mm²) | Current Capacity (A) | Tensile Strength (kN) | Weight (kg/km) |
---|---|---|---|---|---|
AAAC 6201 | 10.0 | 50 | 180 | 14.7 | 137 |
AAAC 6061 | 12.5 | 70 | 230 | 20.3 | 192 |
AAAC 6063 | 15.0 | 100 | 280 | 29.0 | 267 |
AAAC 6082 | 17.5 | 125 | 330 | 37.3 | 330 |
Detailed Applications
- 6201 Aluminum Alloy: Electrical conductors and fuses due to its high conductivity and strength.
- 6061 Aluminum Alloy: Heavy-duty applications requiring good corrosion resistance, such as railroad cars, bridges, pipelines, aerospace structures, trucks, marine applications, storage tanks, and furniture.
- 6063 Aluminum Alloy: Architectural applications, including windows, doors, storefronts, trim items, furniture, and pipe railings.
- 6082 Aluminum Alloy: High-stress applications, such as trusses, bridges, cranes, transport applications, ore skips, beer barrels, and milk churns.
- 7005 Aluminum Alloy: Manufacturing consumer electronics and sporting goods, such as laptop shells, mobile phone cases, baseball bats, and golf clubs, due to its excellent stress resistance and weldability.
- 7050 Aluminum Alloy: Aerospace industries for fuselages, medium and thick plane plates, ribs, rivets, and other aircraft components, due to its high strength and corrosion resistance.
- 7075 Aluminum Alloy: Items requiring high strength and corrosion resistance, such as the skin, rivets, panels, frames, and stringers of aircraft, as well as baseball bats, ski poles, and other sports equipment.
Summary
AAAC conductors, due to their high strength, better sag characteristics, improved electrical properties, and excellent corrosion resistance, are highly suitable for various transmission and distribution applications, particularly in harsh environmental conditions.
For more detailed information, refer to the full articles: